Note. Before removing the pistons and connecting rods, remove the cylinder head, oil pan and upper (aluminum) oil pan section (see chapter 2A or 2B). In addition, on four-cylinder engines, remove the balancer shafts (see paragraph 9).
1. Check the surface of the cylinder with your fingernail: if a ridge has formed on the upper edge of the zone of movement of the rings during the reciprocating movement of the piston in the cylinder (approximately 6 mm from the top of each cylinder). If carbon deposits or cylinder wear have caused the ridge to form, it should be completely removed with a special tool (pic. 10.1). Follow the instrument manufacturer's instructions. If the ridges are not removed before removing the piston and connecting rod assemblies, the piston may break.
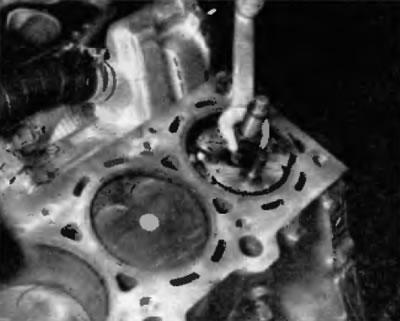
Pic. 10.1. Before removing the pistons, use a suitable reamer to remove the ridges in the upper area of the cylinder
2. After removing the ridges in the cylinders, turn the engine over so that the crankshaft is on top.
3. Before removal of pistons in gathering with rods by means of probe check up axial backlashes in heads of rods. Insert a feeler gauge between the first connecting rod and the thrust surface of the crankshaft (pic. 10.3). The probe should slide into a snug fit. Repeat this procedure on each connecting rod. The axial clearance is equal to the stylus thickness. Ask a workshop for the service limit value for the gap. If the clearance exceeds the service limit, new connecting rods will be required. If new connecting rods are installed (or new crankshaft), the axial clearance may be less than the minimum allowable value. In this case, the connecting rods will need to be machined to restore the correct clearance. If necessary, consult a specialized service station.
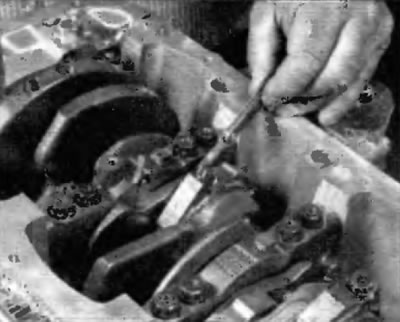
Pic. 10.3. Check axial clearances in connecting rods
4. Check connecting rods and caps for identification markings (pic. 10.4). If not clearly marked, punch the appropriate number of dots on each connecting rod and corresponding cap (1, 2, 3, etc., depending on the cylinder to which they refer).
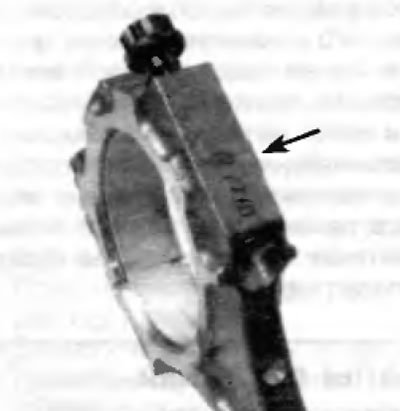
Pic. 10.4. If the connecting rods and connecting rod bearing caps are unmarked, mark the corresponding cylinder numbers on the bearing caps. Do not confuse the markings shown here with the connecting rod numbers; this is the bearing size identification mark
5. Loosen each of the connecting rod bearing cap bolts, unscrewing not ½ turn at a time, until the bolts can be unscrewed by hand. Remove the #1 connecting rod bearing cap and corresponding bearing shell. Do not remove the bearing shell from the cover.
6. Remove the bearing shell and pull the piston and connecting rod assembly through the top of the engine. Use a wooden or plastic hammer handle to press down on the seating surface for the top bearing in the connecting rod.
7. If resistance is felt, check again to see if the comb is completely removed from the cylinder.
8. Repeat the procedure on the remaining cylinders.
9. After removal, assemble the caps and bearing shells of the connecting rods with the corresponding connecting rods, screw in the bolts and tighten them by hand. Leaving the old bearing shells in place until reassembly will help prevent accidental damage to the running surfaces in the connecting rods.
10. Pistons and connecting rods are now ready for inspection and repair, which should be carried out at a service station.
Installation of piston rings
11. Before installing new piston rings, check the gaps in the locks of the rings. It is assumed that the piston ring gap in the groove has already been checked and found to be correct.
Note. Pistons and connecting rods can only be installed after installing the crankshaft (see paragraph 11).
12. Lay out piston assemblies with connecting rods and new sets of rings so that when measuring gaps in the joint and assembling the engine, sets of rings are consistent with the same piston and cylinder
13. Insert the top (№1) ring into the first cylinder and position it perpendicular to the walls of the cylinder, pressing it with the piston head (pic. 10.13). The ring should be located near the base of the cylinder, on the lower edge of the ring travel zone.
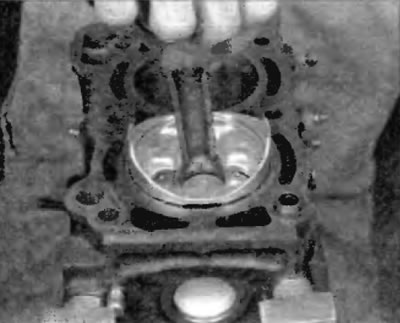
Pic. 10.13. Insert the top ring of the cylinder, and then use the piston to push it down to the specified depth so that the ring is not warped in the cylinder
14. To measure the gap in the joint, insert a feeler gauge between the ends of the ring lock until you find the feeler gauge, the thickness of which is equal to the width of the gap (pic. 10.14). The probe should enter between the ends of the ring lock with little resistance. Consult your dealer for the correct keyhole clearance for your specific engine. If the gap is over or under specification, check again that the correct type of rings are being used before proceeding.
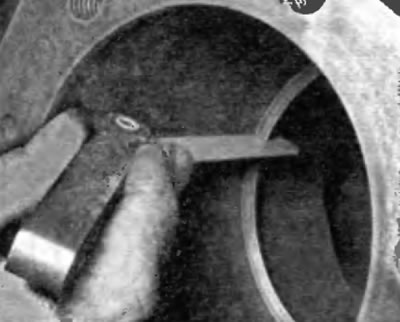
Pic. 10.14. With the ring perpendicular to the walls of the cylinder, measure the gap in the lock of the ring with a feeler gauge
15. If the gap is too small, it should be increased, otherwise the ends of the ring lock may come into contact with each other when the engine is running, which can lead to serious damage to the engine. The gap in the lock can be increased by very carefully sawing the ends of the joint with a small file. Clamp the file in a soft-jawed vise and slide the ring over the file so that the ends of the ring are in contact with the surface of the file. Then slowly move the ring to remove the material from the ends. When performing this operation, move the ring only from the outer edge of the clamped file in the direction of the vise (pic. 10.15).
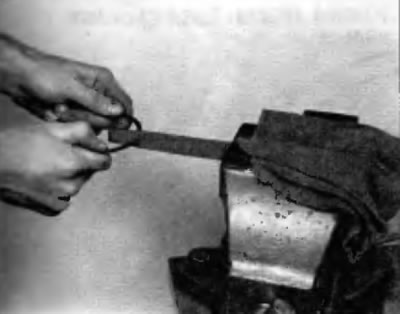
Pic. 10.15. If the ring lock clearance is too small, clamp the file in a vise as shown and file the ends of the piston ring lock. Take care to ensure the parallelism of the welded ends and remove all irregularities and burrs with a needle file
18. Increased clearance in the lock is not critical if it does not exceed approximately 1 mm. Check again that the type of ring you are using is correct.
17. Repeat the procedure for each ring to be installed in cylinder #1 and for each ring in the remaining cylinders. Don't forget about keeping the rings, pistons and cylinders in line.
18. After checking the gaps in the locks of the rings and making the necessary adjustments, the rings can be installed on the pistons.
Application. On V6 engines, the pistons for the left bank of cylinders are marked with either the letter L or a single round mark on the front of the piston. The pistons for the first row of cylinders are marked with either the letter R or two round marks on the front of the piston.
19. Usually the oil scraper ring is installed first (the bottom of the piston). It consists of three separate elements. Insert the expansion element into the groove (pic. 10.19, a). If there is a protrusion that prevents the ring from rotating, insert it into the hole drilled in the groove. Then install the upper element of the ring in the same way (pic. 10.19, b). Do not use a piston ring installer on the end pieces of the oil scraper ring as they may be damaged. Instead, insert one end of this end piece into the gap between the spacer/expander and groove wall, hold it securely in place, and run your finger around the perimeter of the piston, pushing the oil ring end piece into the groove. Finally, install the bottom ring element.
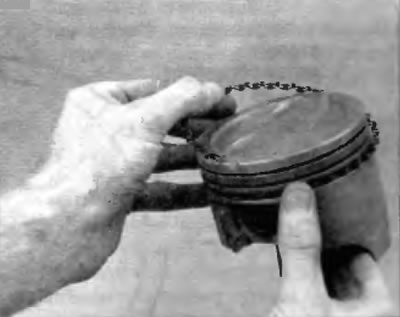
Ras. 10.19 a. Installing the spacer/expansion ring in the oil scraper groove
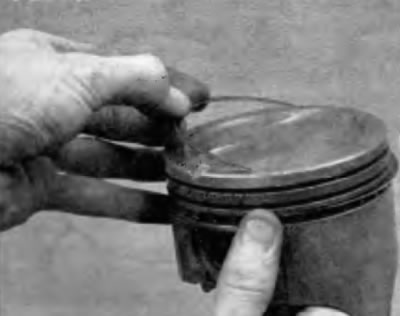
Pic. 10.19, b. Do not use a piston ring installer to install the upper and lower oil ring elements
20. After installing the three elements of the oil scraper ring, make sure that both the upper and lower ring elements can rotate freely and smoothly in their respective grooves.
21. Ring number 2 is installed next (average). It is usually stamped with a marking that should face the piston crown. Do not confuse the top and middle rings as they have different cross sections.
Note. Be sure to follow the instructions given on the packaging of the rings. Different manufacturers may prescribe different installation methods.
22. Use a piston ring installer and make sure the marking is facing the piston crown, then insert the ring into the middle groove on the piston (pic. 10.22). Do not expand the ring more than is really necessary to put it on the piston.
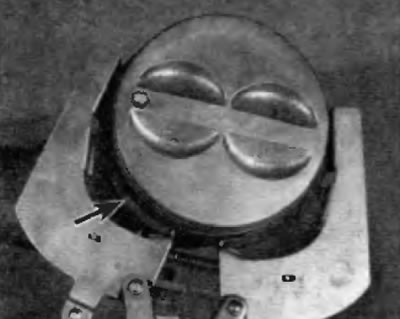
Pic. 10.22. Use a special tool to install piston rings #2 to #1 (top). Make sure that the alignment mark on the piston ring (Oh) facing the bottom of the piston
23. Install ring #1 in the same way (upper). Make sure the label is facing up. Be careful not to confuse rings #1 and #2.
24. Repeat the procedure for the remaining pistons and rings.