Check on the engine
1. Check the performance of the nozzles by ear.
A) With the engine running or when turning it over with a starter, use a phonendoscope to make sure by ear (sound of injected fuel) in the performance of the injectors, making sure that the frequency of injections is proportional to the frequency of rotation of the engine crankshaft.
b) In the absence of a phonendoscope, you can check the performance of the nozzles by touching them with your finger or a screwdriver.
If there is no sound or if it is unusual in nature, check the wiring, connector, injector, additional injector resistance, or the presence of a control signal from the electronic control unit.
2. Check the injector resistance. Disconnect the injector connector and using an ohmmeter, measure the resistance of the injector.
- Rated resistance at 20°C - 13.4-14.2 Ohm
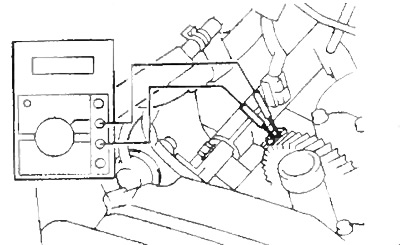
If the resistance value is out of range, replace the injector. Connect the injector connector.
Removing nozzles
1. Disconnect (-) wire from the negative battery terminal.
2. Disconnect the accelerator cable and throttle cable (from automatic transmission).
3. Remove the bracket and coolant bypass hoses.
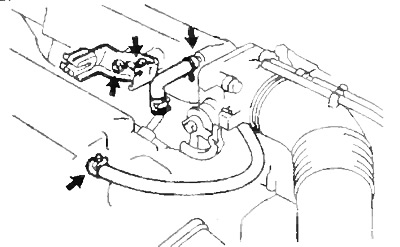
4. Disconnect the power steering hoses and remove the wiring protection.
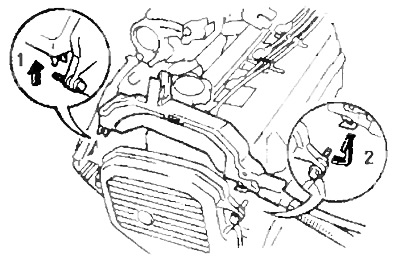
5. Turn out 4 caps from a head of the block of cylinders and take consolidations.
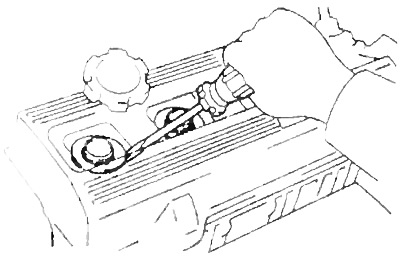
6. Disconnect the injector connectors.
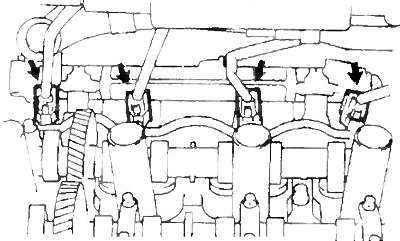
7. Remove the fuel manifold and injectors.
A) Turn away bolts of fastening of a fuel collector to a head of the block of cylinders.
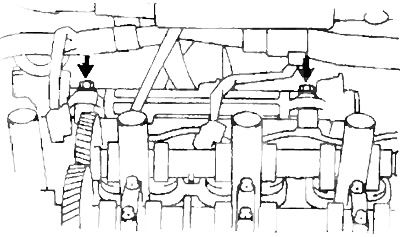
b) Remove the fuel manifold along with the injectors.
Note: handle nozzles carefully and do not let them fall.
V) Remove the insulators and spacers from the cylinder head.
G) Remove the four injectors from the fuel manifold.
d) Remove the O-ring and safety sleeve from each nozzle.
Checking the injectors
1. Inspect the nozzles, use a match to check for dirt on the inlet mesh, if there is, blow it out with air.
2. Check the quality of the injection nozzles.
Note: Avoid sparks during testing. Keep a fire extinguisher ready.
A) Prepare the necessary service tools and assemble a circuit to test the injectors.
b) Install the nozzle in a measuring container. Attach a suitable vinyl hose to the injector to prevent fuel splashing.
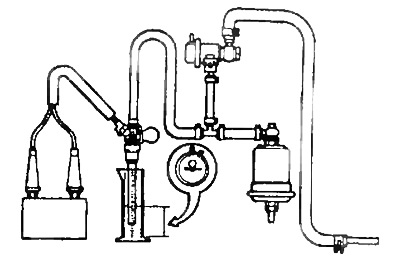
Injector test scheme
V) Connect the wire to the negative (-) terminal to the battery and turn on the ignition.
Note: do not start the engine.
G) Jumper short the leads "FP" and +V" diagnostic socket.
To) Connect the service wire to the injector and battery for 15 seconds, measure the volume of fuel injected into the measuring vessel. Repeat the test 2-3 times for each injector.
- The volume of injected fuel - 49-52 cm3 for 15 s
- The difference in flow between nozzles is up to 5 cm3
If the fuel supply is out of range, replace the injector.
d) At the end of the previous check, disconnect the wires from the battery and check for fuel leakage through the injector.
Leak no more than 1 drop in 1 minute
Installation of nozzles
1. Install injectors and fuel manifold.
A) Install a new sealing sleeve on the injector (if filmed).
b) Apply a thin layer of fuel (lithol) on a new O-ring and install it on the injector.
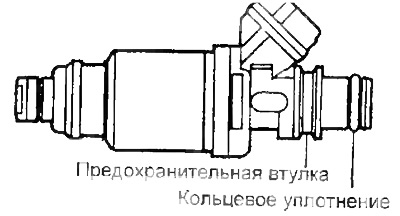
V) Rotate the injectors and insert them into the fuel manifold.
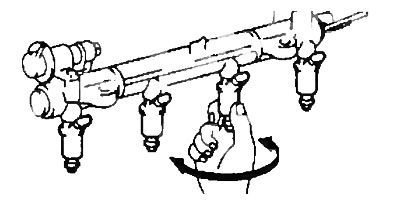
G) Install (better stick it) insulators and spacers.
d) Install the injectors together with the fuel manifold on the intake manifold. Gradually tighten the fuel rail to intake manifold bolts.
e) Make sure the injectors turn without sticking in their seats.
Note: If the nozzles do not turn, the O-rings may not be properly installed. Replace o-rings.
and) Install the injectors so that their connectors are on top.
h) Bolt the fuel manifold to the cylinder head.
- Tightening torque - 17 Nm
2. Connect the electrical connectors of the injectors.
3. Apply sealant to the cylinder head as shown.
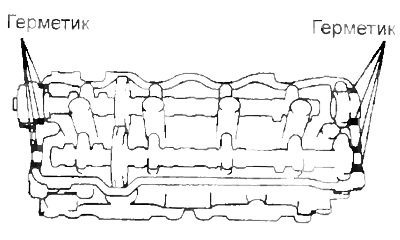
4. Install the caps and seals in the cylinder head cover.
- Tightening torque - 23 Nm
5. Install wiring protection and connect power steering hose.
6. Connect the coolant bypass hoses and install the bracket.
7. Connect the accelerator cable and the throttle cable from the automatic transmission.